What are the processes involved in the sheet metal processing of chassis and cabinets?
Release time:
2025-01-07
【Summary】The sheet metal processing of chassis and cabinets is a complex process involving multiple steps. Below is its basic flow:
Sheet Metal ProcessingChassis and Cabinetis a complex process involving multiple steps. The following is its basic flow:
1. Design Stage
- According to customer requirements and drawings, use design software such as CAD to design the size, shape, and structure of the sheet metal parts to be processed, forming processing decomposition diagrams and assembly diagrams.
2. Material Preparation
- Select suitable sheet metal materials according to design requirements. Common materials used in sheet metal processing include cold-rolled plates (SPCC), hot-rolled plates (SHCC), galvanized plates (SECC, SGCC), copper (CU, including brass, purple copper, beryllium copper), aluminum plates (such as 6061, 6063, hard aluminum, etc.), aluminum profiles, stainless steel (including mirror, brushed, matte), etc.
- Material selection usually needs to consider the product's Applications and cost. For example, cold-rolled plates have low cost, are easy to form, and have a material thickness of ≤3.2mm, mainly used for electroplating and baking paint parts; hot-rolled plates have a material thickness of T≥3.0mm, low cost, but are difficult to form, mainly used for flat parts.
3. Processing
- Cutting: Use laser cutting machines, mechanical shears, CNC punching machines (turret CNC punching machines), and other equipment to cut metal sheets into corresponding shapes and sizes according to design requirements. Laser cutting machines can cut materials such as carbon steel and stainless steel, with neat, smooth, and beautiful cross-sections, and precise dimensions, especially suitable for workpieces with curves. CNC punching machines are mainly aimed at workpieces with thinner processing materials (generally below 2.5mm), with many holes or requiring special molds for processing, having certain cost advantages when in large batches.
- Bending: Use bending machines to bend the cut plates into preset angles and shapes. After the material is prepared, if most need to be bent, multiple computer bending machines can be used for fast and precise processing. Bending should follow the order from inside to outside, from small to large, and from special to general, to avoid interference with subsequent processes.
- Stamping: Use stamping machines and other equipment for stamping operations, such as punching, cutting corners, blanking, punching convex packages (bumps), tearing, drawing holes, forming, etc. This requires corresponding molds to complete the operations, such as punching and blanking molds, convex package molds, tearing molds, drawing hole molds, forming molds, etc.
- Welding: For parts that need to be connected, use methods such as argon arc welding, spot welding, carbon dioxide welding, laser welding, resistance welding, and TOX riveting for welding. After welding, the workpiece is polished to make it more solid and beautiful.
4. Surface Treatment
-
Perform surface treatment on the processed sheet metal parts to enhance their appearance quality and corrosion resistance. Common surface treatment methods include:
- Electrostatic Powder Coating: Mainly for carbon steel workpieces, first degrease, derust, clean the surface, and phosphatize, then perform electrostatic powder coating and high-temperature baking. The treated workpiece has a beautiful surface, will not rust for several years, and is cost-effective.
- Liquid Paint: Generally used for large workpieces that cannot be moved, with advantages of convenience and low cost. Usually carried out in two steps, first applying a primer and then a topcoat.
- Electroplating: Includes electro-galvanizing and hot-dip galvanizing, which can form a layer of metal coating on the surface of the sheet metal, serving to prevent corrosion and beautify. Electro-galvanizing has a bright and smooth appearance, with a thinner zinc layer; hot-dip galvanizing has a thicker zinc layer and can produce a zinc-iron alloy layer, with stronger corrosion resistance than electro-galvanizing.
- Surface Oxidation: The surface anodizing of aluminum and aluminum alloys can be oxidized into various colors, serving protective and decorative purposes. At the same time, an anodic oxidation film can be formed on the surface of the material, which has high hardness and wear resistance, as well as good electrical insulation and thermal insulation.
- Surface Brushing: Place the material between the upper and lower rollers of the brushing machine, driven by a motor, allowing the material to pass through the upper and lower sanding belts, creating streaks on the surface of the material to beautify its appearance. This surface treatment method is usually used for aluminum materials.
- Silk Screen Printing: A process of printing various labels on the surface of the material, generally using flat silk screen printing and transfer printing methods. Flat silk screen printing is mainly used on general flat surfaces, but if there are deeper pits, transfer printing is required.
5. Assembly Stage
- Assemble all the processed sheet metal parts into a complete product according to design requirements.
6. Quality Inspection
- Conduct strict quality inspection on the final processed sheet metal products, including checks on dimensions, shapes, appearances, and performance, to ensure they meet design requirements and quality standards.
In summary, the steps of sheet metal processing include the design stage, material preparation, processing, surface treatment, assembly stage, and quality inspection. Each step has its specific processes and requirements to ensure the quality and performance of the final product.
TAG:
RELATED INFORMATION
2025-01-20
How much do you know about stainless steel sheet metal processing?
2025-01-18
What are the inspection standards for sheet metal processing chassis and cabinets?
2025-01-17
What are the main processes of sheet metal processing?
2025-01-16
What is the process flow of the chassis cabinet?
FAX
ADD
Gengguantun Industrial Development Zone, Qingxian County, Hebei Province, China
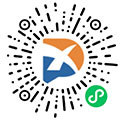
WeChat applet