Machining Process Flow
Release time:
2025-01-08
【Summary】The machining process is an important step in the manufacturing of workpieces or parts. It uses mechanical processing methods to directly change the shape, Size, and surface quality of the blank, making it a qualified part. Below is a detailed introduction to the machining process:
MachiningThe process flow is an important step in the manufacturing and processing of workpieces or parts. It uses machining methods to directly change the shape, size, and surface quality of the blank, making it a qualified part. Below is a detailed introduction to the machining process flow:
1. Processing Design
According to product requirements, design the drawings of the parts, clarifying the technical requirements such as the shape, size, materials, etc. of the parts. This is the starting point of the machining process flow and the basis for subsequent processing operations.
2. Processing Preparation
- Select the blank: According to the part drawings and processing technology requirements, select suitable blank materials. The selection of the blank should consider factors such as material performance, machinability, and economy.
- Prepare tools, fixtures, measuring tools, etc.: According to processing requirements, select suitable tools, fixtures, and measuring tools. The selection of tools should consider cutting efficiency, processing accuracy, and surface quality; the selection of fixtures should ensure the position and stability of the parts during processing; the selection of measuring tools should meet the requirements of measurement accuracy and efficiency.
- Equipment Debugging: Debug the equipment before processing to ensure that the equipment's accuracy and stability meet processing requirements. This includes checking the operating status of the equipment, adjusting the parameters of the equipment, and conducting necessary trial runs.
3. Formulate Processing Technology Regulations
Processing technology regulations are technical documents that specify the mechanical processing technology processes and operating methods for parts. When formulating processing technology regulations, the following factors need to be considered:
- Calculate the annual production plan and determine the production type: Based on the annual output and similar characteristics of the parts, determine the production and organization form of the parts.
- Analyze part drawings and product assembly drawings: Conduct process analysis on the parts to understand the structural characteristics, technical requirements, and assembly relationships of the parts.
- Draft the process route: Based on the processing requirements of the parts and the existing equipment conditions, draft a reasonable process route. The drafting of the process route should consider factors such as processing sequence, processing methods, processing allowances, and heat treatment.
- Determine the processing allowance for each process, calculate process dimensions and tolerances: According to the part drawings and processing technology requirements, determine the processing allowance and process dimensions and tolerances for each process. This is key to ensuring the processing accuracy and surface quality of the parts.
- Determine cutting parameters and labor time quotas: Based on factors such as processing materials, tool performance, and equipment conditions, determine reasonable cutting parameters and labor time quotas. The selection of cutting parameters should consider cutting efficiency, processing accuracy, and surface quality; the formulation of labor time quotas should consider production efficiency and cost control requirements.
4. Processing Operations
Carry out cutting, grinding, and other processing operations according to the processing technology regulations and CNC programs (if necessary). During the processing, the following points need to be noted:
- Closely monitor the operating status of the machine tool: Ensure that the machine tool operates smoothly, without abnormal vibrations or noises.
- Control cutting parameters: Adjust cutting speed, feed rate, and cutting depth reasonably according to processing technology regulations and actual conditions.
- Ensure processing quality: During processing, it is necessary to closely monitor the processing conditions of the parts, promptly identify and resolve issues during processing, such as tool wear and insufficient cutting fluid. Additionally, the processed parts need to be inspected, including checks on dimensional accuracy, shape accuracy, and surface roughness, to ensure that the part quality meets design requirements.
5. Subsequent Processing
- Handle processing waste and cutting fluid: Some waste and cutting fluid will be generated during processing, which needs to be handled in a timely manner. Waste can be recycled or discarded; cutting fluid needs to be purified or reused to avoid environmental pollution.
- Record and organize processing data: In the machining process flow, recording and organizing processing data is also a very important step. This data can include processing time, cutting parameters, inspection results, etc., which helps analyze problems in the processing process, optimize processing plans, and improve processing efficiency and quality.
In summary, the machining process flow is a complex and detailed process that requires strict adherence to processing technology regulations and operating procedures. Through reasonable process arrangements and advanced processing technologies, production efficiency can be improved, production costs can be reduced, and the processing accuracy and surface quality of parts can meet design requirements.
TAG:
RELATED INFORMATION
2025-01-20
How much do you know about stainless steel sheet metal processing?
2025-01-18
What are the inspection standards for sheet metal processing chassis and cabinets?
2025-01-17
What are the main processes of sheet metal processing?
2025-01-16
What is the process flow of the chassis cabinet?
FAX
ADD
Gengguantun Industrial Development Zone, Qingxian County, Hebei Province, China
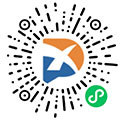
WeChat applet